Instructables – I made this electric guitar at my high school shop and at home with standard machines and hand tools, it was an amazing project and took me a little over a school year to source the materials, buy, plan, and create the entire guitar but I’m very happy with the end result. I bought all the electronics and small pieces of hardware online through amazon.ca and I bought the wood at a local specialty wood store, totaling approx. $500 (a little expensive due to some faulty deliveries, shipping costs, the wood, and the DiMarzio mini humbucker neck pickup). I styled this guitar after a fender telecaster but took some liberties in making it my own during the build in several different ways, such as the contouring, pickup layout, through body electronics, back plate, finish and wood (Black Limba body, curly/bird’s eye maple neck, ebony fretboard, walnut back).Add TipAsk QuestionCommentDownload
Step 1: Dream and Design
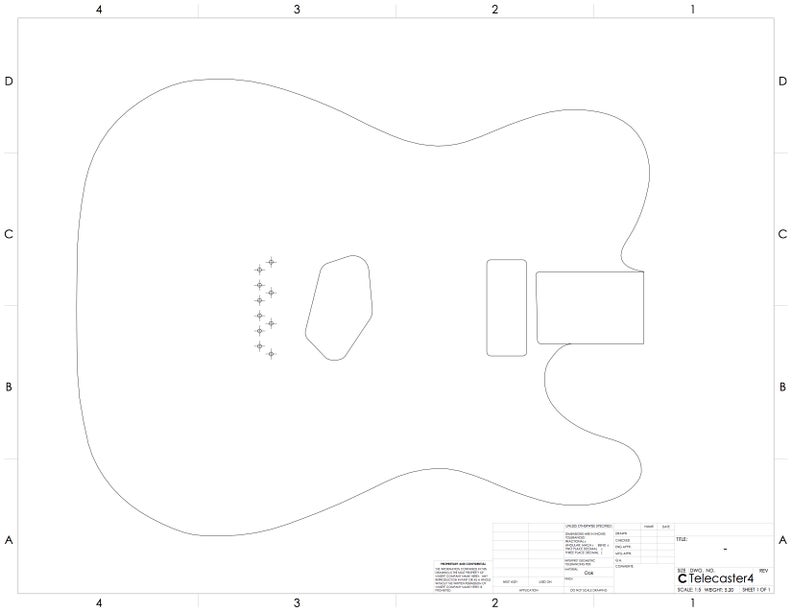
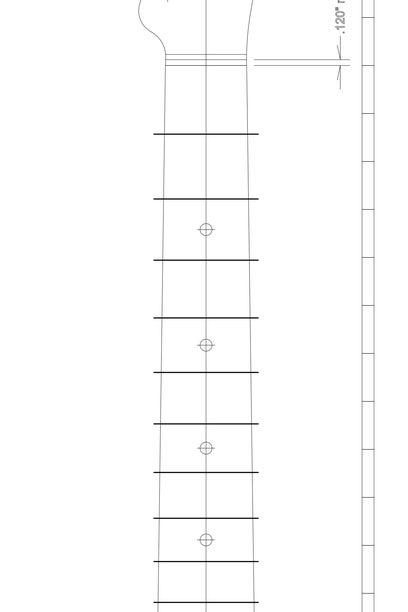
I started this build by doing a lot of research into what I wanted to achieve. This project originally started out as a hobby, so I don’t have pictures of the original drawings, but I went to my local guitar shop for inspiration, online forums, google images, and brainstormed on a notebook. Eventually, I used Solidworks to create a 3D model of the guitar body to use as a template for making it later on. I left out the contouring in the drawing to make it less complicated for the plywood template. The image of the neck I took off of a guitar forum (quick google search) and printed both of these drawings 1:1 scale on a large printer we have at the school. If this is not possible, I know that there were Telecaster and Stratocaster templates for sale at the specialty wood store where I bought my wood, or you could print out each quadrant onto separate pieces of paper and do it that way.Add TipAsk QuestionCommentDownload
Step 2: Body Template
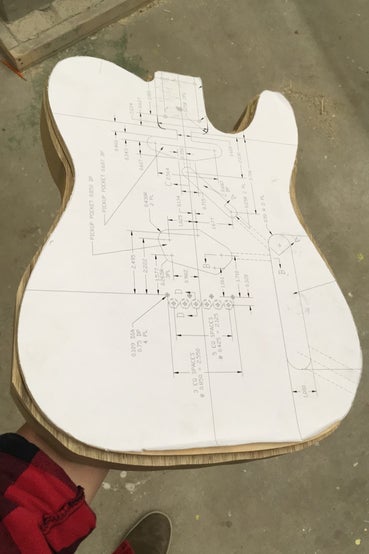
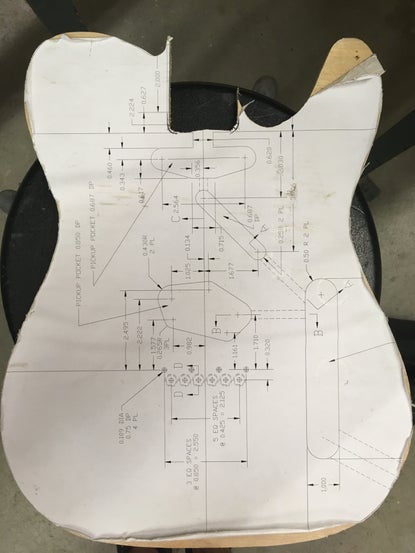
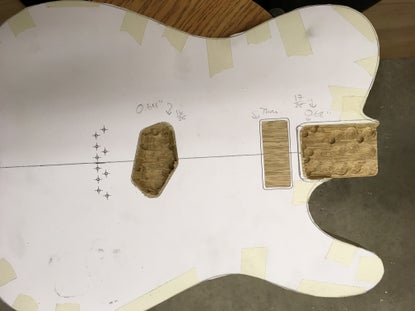
I used adhesive spray to tack the printed template onto a piece of plywood, then used a bandsaw and a spindle sander to fix the edge to exactly what I wanted, I used this method because if I made a mistake, I could restart easily, it would be easier to use the router table on a template, and it would make the outside more uniform. I then printed another template and used adhesive spray to adhere it to the body blank, then roughly cut out the body blank within 1/4″ for the router table. I used a long 1/2″ router bit with a roller at the base instead of the top which I bought online as well, I don’t have a picture of it here, though.Add TipAsk QuestionCommentDownload
Step 3: Refining the Neck Blank
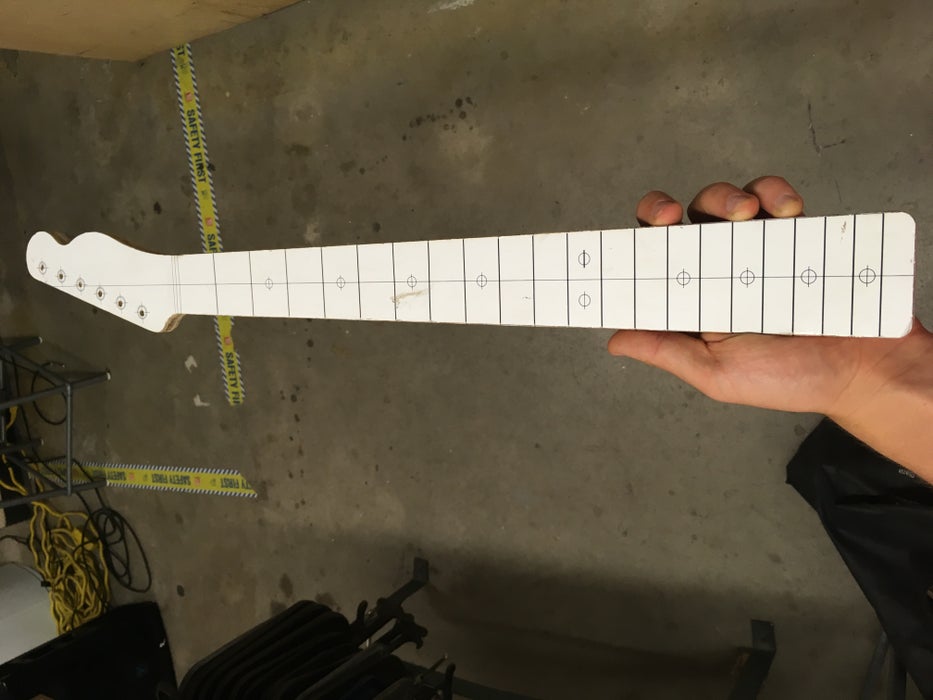
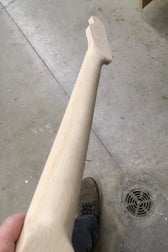
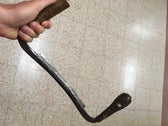
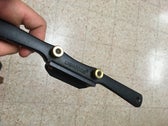
I did the same template technique on the neck blank, a piece of curly maple. Careful note that on the router table, make sure to leave the end grain and sand it instead on thinner sections, I ripped part of the headstock but was able to glue it back seamlessly. In this step I also used a spare piece of wood as a jig to create the slot for the truss rod which sat underneath the fretboard and was accessed at the base (more details on that later). I used my great great great grandfathers drawknife to round the neck roughly (still works great), then a smaller drawknife-style plane for finer work then finished it with rising degrees of sandpaper.Add TipAsk QuestionCommentDownload
Step 4: Making the Fretboard
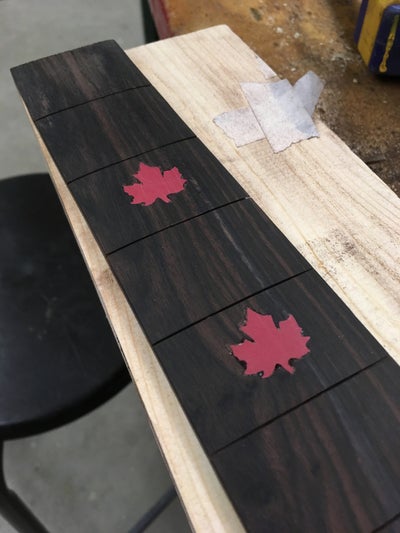
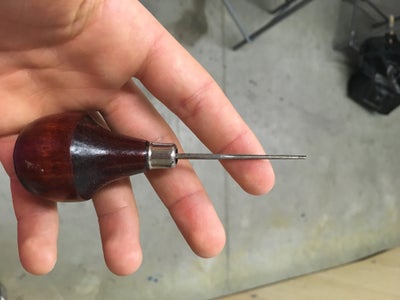
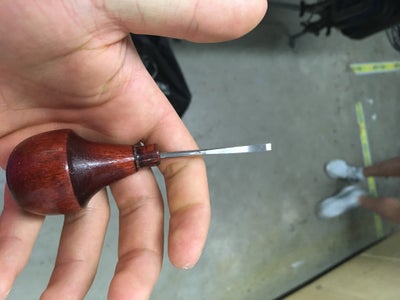
Probably the most painstaking part of this build was inlaying the fret markers and frets. For the fret markers, which I bought at the specialty wood store with my wood, I traced and carefully used this tiny chisel and gouge to remove the material by hand and glued the markers in with super glue. To fill small gaps, I mixed a small bit of super glue with wood dust from the fretboard. I did this before sanding the 9″ contour on the fretboard because then it would seamlessly blend with the surface.Add TipAsk QuestionCommentDownload
Step 5: Contouring the Fretboard
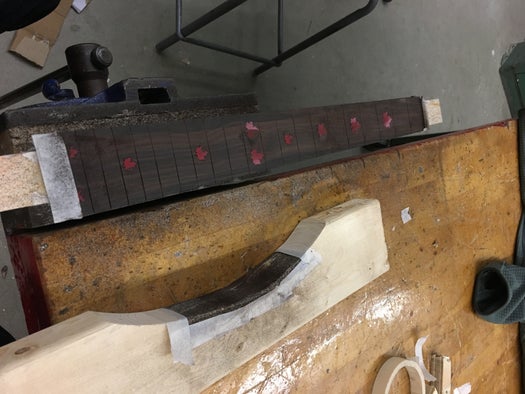
I used a string and a nail to sketch a 9″ radius circle onto a makeshift sanding block to contour the fretboard, then used a lot of elbow grease to finish the job.Add TipAsk QuestionCommentDownload
Step 6: Slotting the Frets
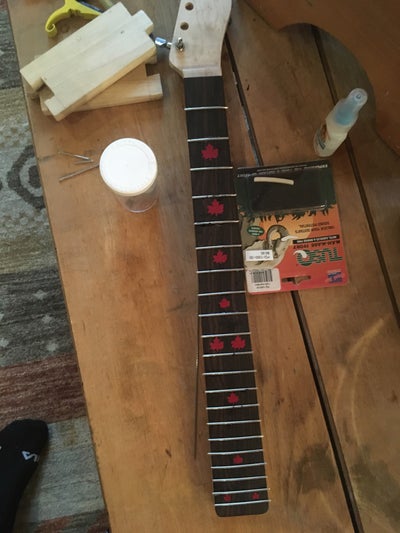
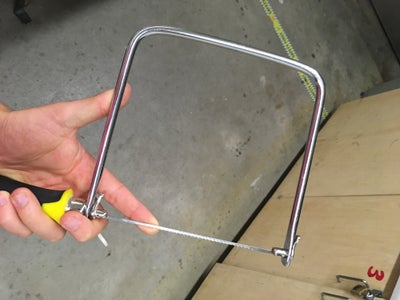
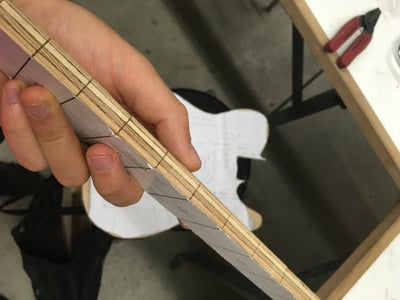
This part of the job was most difficult and probably could have been done better, as I had to re-level the frets later on. I used a coping saw because I didn’t want to buy a fret-cutting saw (which seemed to work out fine) but if you can get a fret saw and a fret dressing tool and a template then do that. I used my plywood template to mark the fret positions and used a caliper to double check them with where I had calculated the fret positions. I leveled the frets using a piece of 1×2 square aluminum tubing as a sanding block.Add TipAsk QuestionCommentDownload
Step 7: Adding the Nut
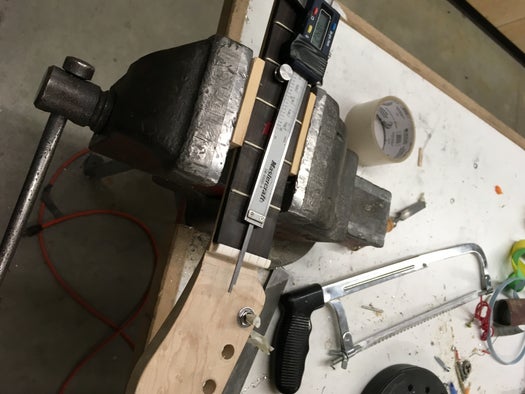
I added a small piece of ebony below my nut to raise it slightly and decided not to add a decorative piece behind. I used a small amount of glue to hold it in place because the strings would eventually hold it down and I might need to replace it later on.Add TipAsk QuestionCommentDownload
Step 8: Routing the Body Cavities
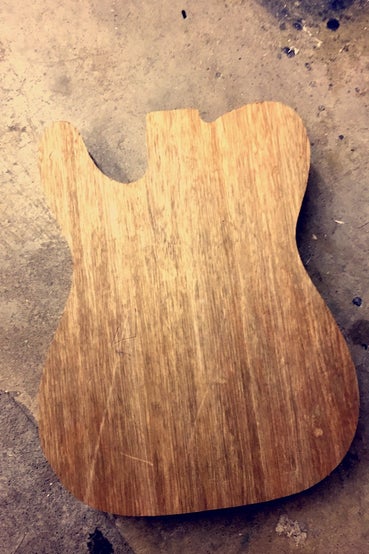
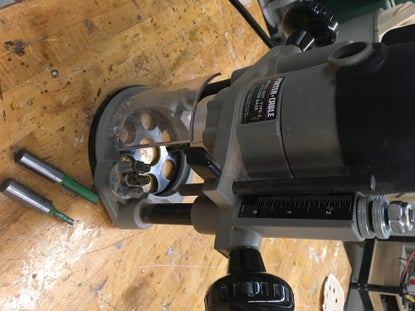
After tracing the outlines of the cavities using the template I printed, I routed the pickup cavities using a portable router by first drilling the cavities roughly and then setting the depth stop. For the neck pickup, a through-body design, I started the cavity and then finished it using the rolling bit on the router table.Add TipAsk QuestionCommentDownload
Step 9: Fitting the Neck and Body Together
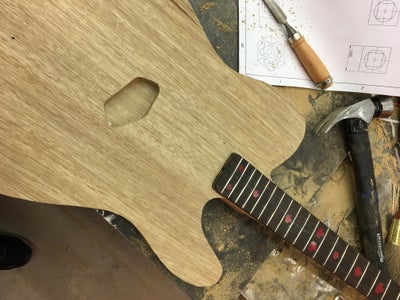
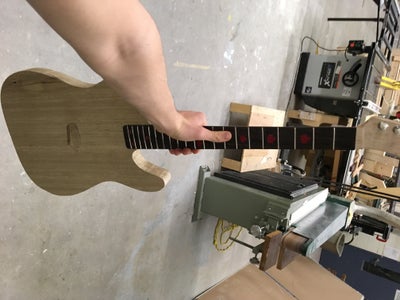
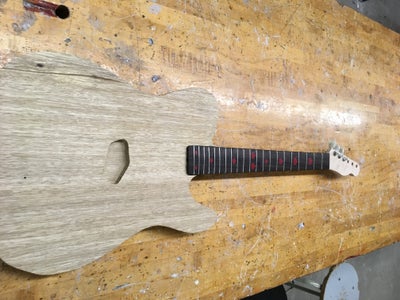
I made the neck first, then fitted the body to the neck because I thought it would be easier than fitting the neck to the body, and it would be better to find any problems now than further along in the project. After a quick test fitting and small adjustments with a chisel, I could continue.Add TipAsk QuestionCommentDownload
Step 10: More Routing!
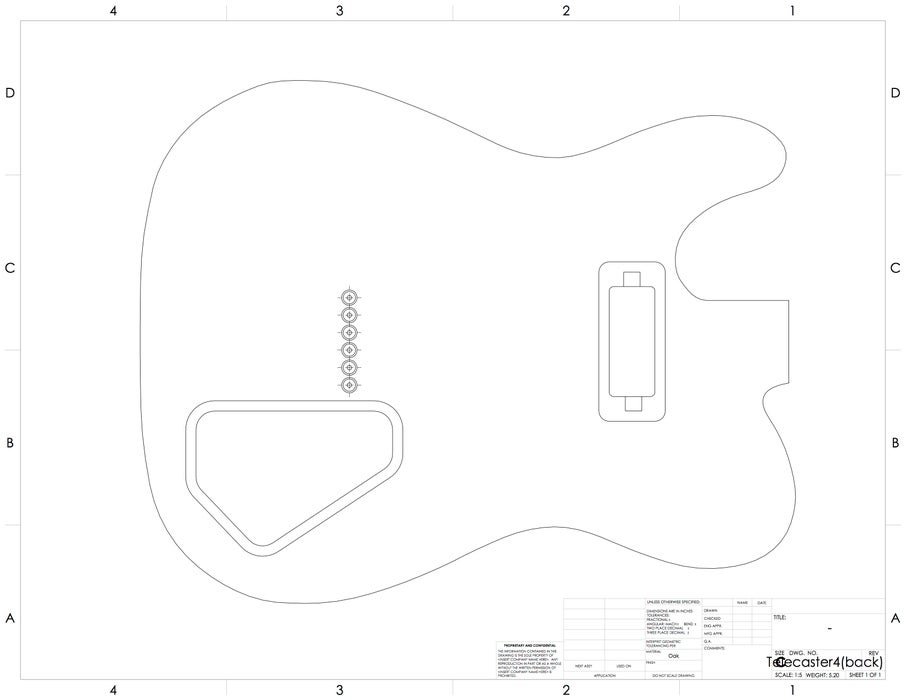
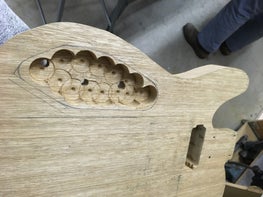
I used the drawing of the back of my 3D model to make a template for the electronics cavity and wiring slots, then continued with the same process as before. I made sure to leave the body contouring until after the routing so I had a flat surface and wouldn’t risk going through the body at any point, there was a lot of clearance, but just to be sure. I went with this method so that the front didn’t need a scratchplate, but all the electronics would still be easily accessible.Add TipAsk QuestionCommentDownload
Step 11: Electronics
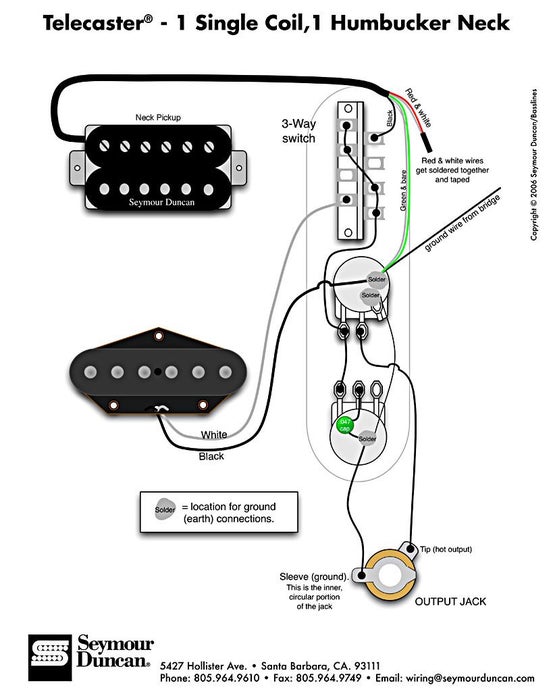
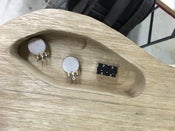
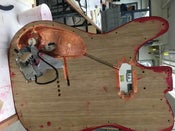
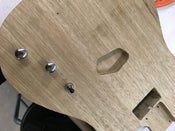
For a first-timer, the electronics were surprisingly easier to figure out than I had anticipated. Using some wiring diagrams I looked up, the main one pictured here, I gathered together all my components and 22 gauge wire, wire strippers, some solder, and a soldering iron, and put it all together after first insulating the entire electronics cavity for ambient noise reduction with copper insulating tape. My three-way switch was slightly cheaper and different than the one pictured in the diagram, so I used a multi-meter to check connectivity to figure out where the pickup wires went. After testing it multiple different ways, I found out that my single coil bridge pickup was garbage, so I had to buy a new one, which worked great after replacing it.Add TipAsk QuestionCommentDownload
Step 12: Making the Back Plate
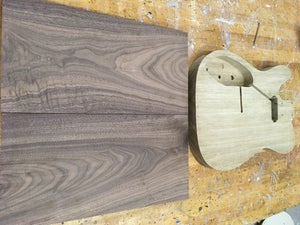
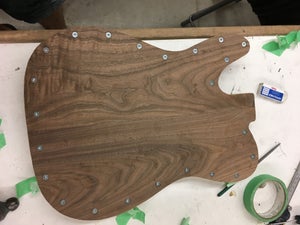
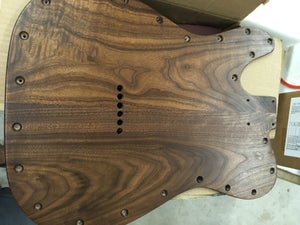
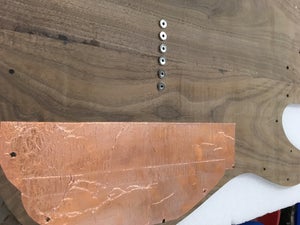
I made my back plate out of walnut from the school shop, which looks really great, and was really cheap. I planed, ripped, and made the rough outline using the school machines, then attached it to the body using wood screws in preparation for the router table (making sure to use a drill press and drill pilot holes, of course) which I think ended up looking super cool. The walnut was only 8″ wide, so I used bar clamps to glue two planed pieces of walnut together. I then added insulation to the section that would be over the electronics cavity, and drilled the holes for the string ferrules on a drill press.Add TipAsk QuestionCommentDownload
Step 13: Testing Finishes
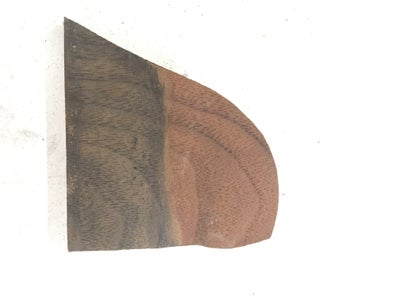
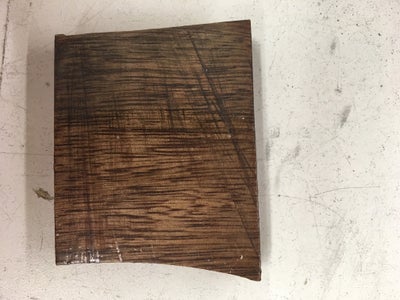
I tried using regular stains on some test pieces, which didn’t work out, so I bought some red stain by Keda which ended out working really great and was super easy to apply and mix with water. I finished the guitar with Solarez grain sealer and UV cure gloss finish, which had a few issues with the application procedure due to the materials I had available to me to apply it but overall it ended up looking great. It was important for me to use test pieces before doing the real thing, as my first go wasn’t the best result.Add TipAsk QuestionCommentDownload
Step 14: Details on Body Finish
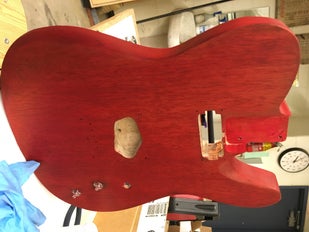
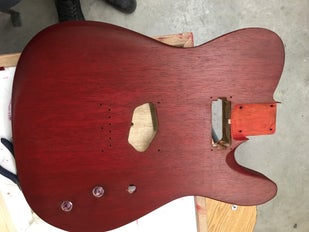
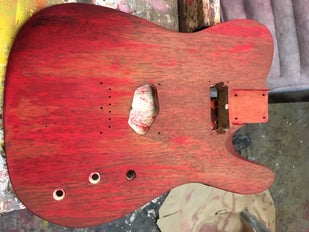
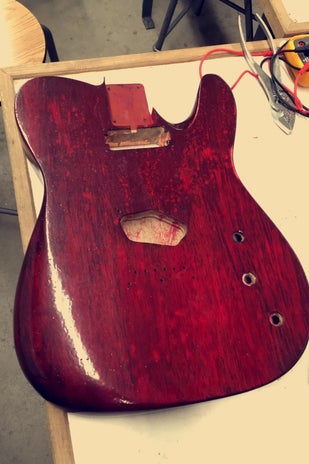
The Keda dye was easy to apply using a paintbrush and a cloth, I added some really deep red dye, and let it dry on the piece instead of wiping it off. It dried purple, so I was a little worried but used the paintbrush to flick and splash some water on it which made it have that cool multi-toned finish which I really enjoy. Between coats of the gloss cure, I sanded the face down and distressed parts of the body with a rotary hand sander, just to get a different look, and to have the reassurance that if I ever scratched it, it wouldn’t be a world-ender.Add TipAsk QuestionCommentDownload
Step 15: Finishing Touches
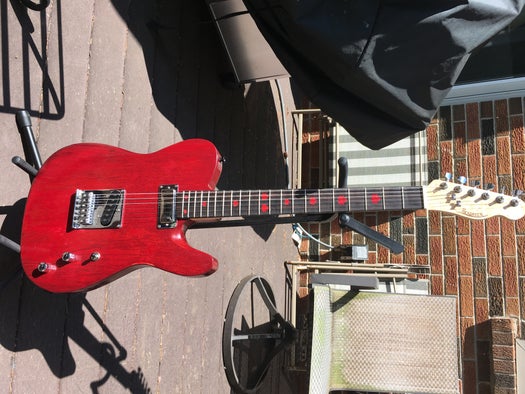
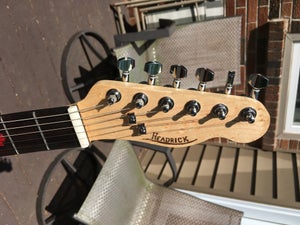
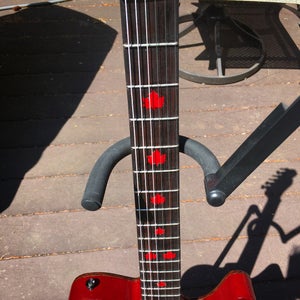
Finally, I wood burned my last name into the headstock, just because, and finished the neck with some wipe-on polyurethane gloss. I wiped off the excess while it was still wet to get a slightly protected neck, but maintained the wood feel and the slide of the neck. The truss rod is accessed just behind the neck pickup, and I can lower the pickup down into the guitar with the strings on because of the through-body design. I then added the strap buttons, the string trees, and strung up the guitar. The end!
Vietnam Plywood – Vietnam Film Faced Plywood