Liny Lamberink – A piece of fence board that cost Kris Ovsenek $3.26 now costs $5 or more
People hoping to finish outdoor home improvement projects this year might be out of luck.
Contractors say they’re postponing major wood deck and fence installations until next year, because a shortage of pressure-treated lumber has been making it tough – and expensive – to source materials over the past few months.
“It’s unbelievable, the shortages we’ve experienced,” said Steve Copp, president of Copp’s Buildall in London. “We’re getting truckloads every week. It’s just not enough to meet demand.”
It’s a trend that’s being felt across the country. The COVID-19 pandemic sparked peoples’ interest in projects around the house, said Copp, but also temporarily shut down lumber mills. Since starting operations again, he said they haven’t been able to keep up.
Kris Ovsenek, the owner of Naklo Carpentry Fence and Deck, said a 1x6x6 fence board used to cost him $3.26. Now, he’s seen lumber yards charge as much as $5 or more for the same piece of wood.
“If you [times] that by a thousand boards for a basic fence job, it’s just unnecessarily expensive. It’s not worth installing a fence at this point.”
Ovsenek said he actually feels uncomfortable selling new jobs, with 50 to 75-per cent increases in the price of lumber.
He said he’s stockpiled enough pressure-treated wood to finish a few bigger projects that he committed to months ago, and he’s focusing his efforts on providing estimates and converting potential customers to alternative materials, such as PVC and vinyl.
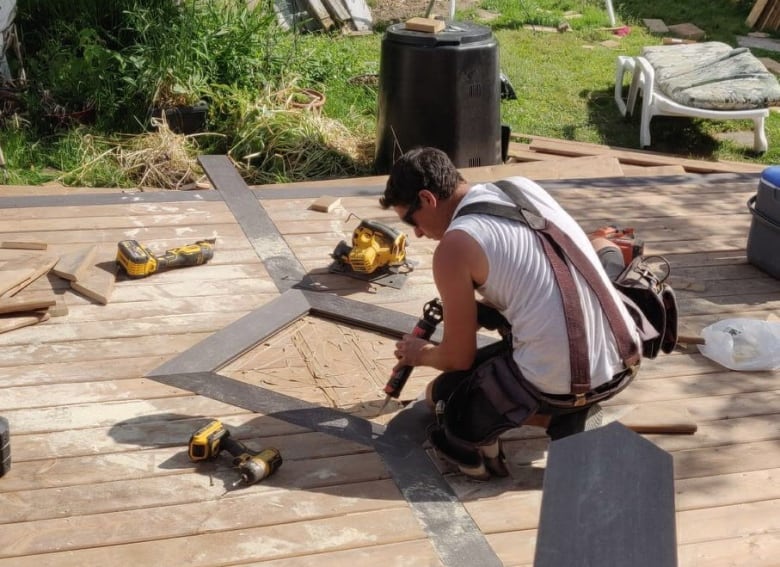
Both Ovsenek and Mike Green, the owner of Indeck Custom Decks, have told prospective clients to wait until next year if they’re committed to using pressure-treated wood, in hopes that supply and demand even out.
“I’ve done a lot of smaller projects this year,” said Green.
Bigger projects take longer to complete because he has to visit several locations to find wood. A two-week project could take as long as four-to-six weeks, he said.
First come first serve
Copp’s Buildall has stopped delivering pressure-treated wood to contractors’ job sites.
“We aren’t delivering right now because we can’t keep up. We’re letting people pick it up as we get it,” said Copp.
On more than one occasion, he said customers have followed transport trucks carrying wood on the highway to their lumber yard.
“It’s basically first-come, first served.”
Copp said if supply troubles continue next year, there might be the opportunity to source wood from Europe instead.
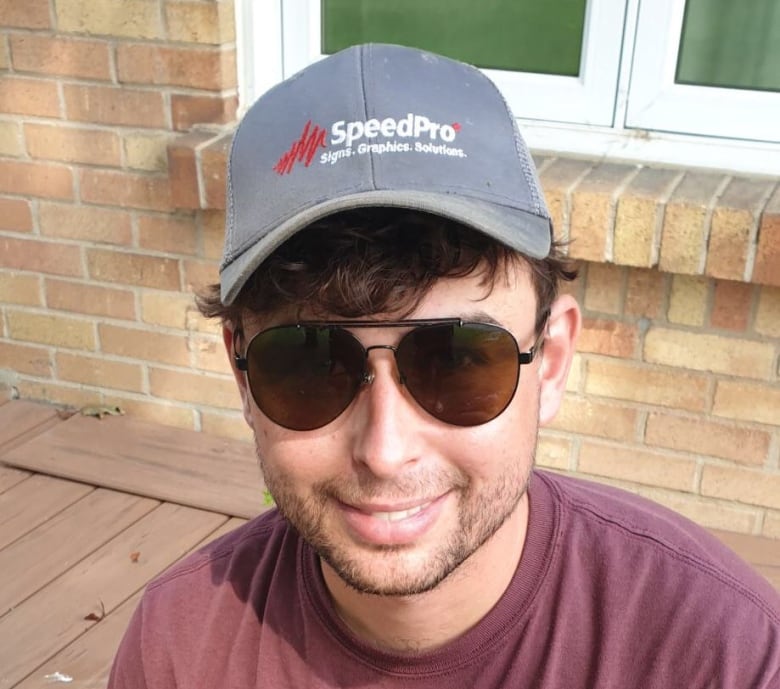
Policies to protect lumber
Ovsenek said small business owners, and even bigger home builders, rely on businesses like Copps, Rona and Moffatt & Powell for their lumber.
“Selfishly, we would hope they wouldn’t sell to as many homeowners as they have been, but from their point of view, if you can sell the material, sell the material.”
He’s calling on the Canadian government to address the shortage, saying it could lead to poor consequences for the economy in the future.
“I believe in capitalism but I also believe, when it comes to national prosperity, that should come first, and definitely for something that’s a natural resource that should belong to all Canadians,” he explained.
“If it means putting policies in place that ensure the lumber supply doesn’t deplete and keeps the Canadian economy moving forward, I think that’s something the Canadian government needs to look into further.”